Abstract: The powder spraying process, also known as powder coating, is a new type of coating process that has developed rapidly in recent decades. For the powder spraying process, there is no doubt that powder saving is the top priority for cost control.
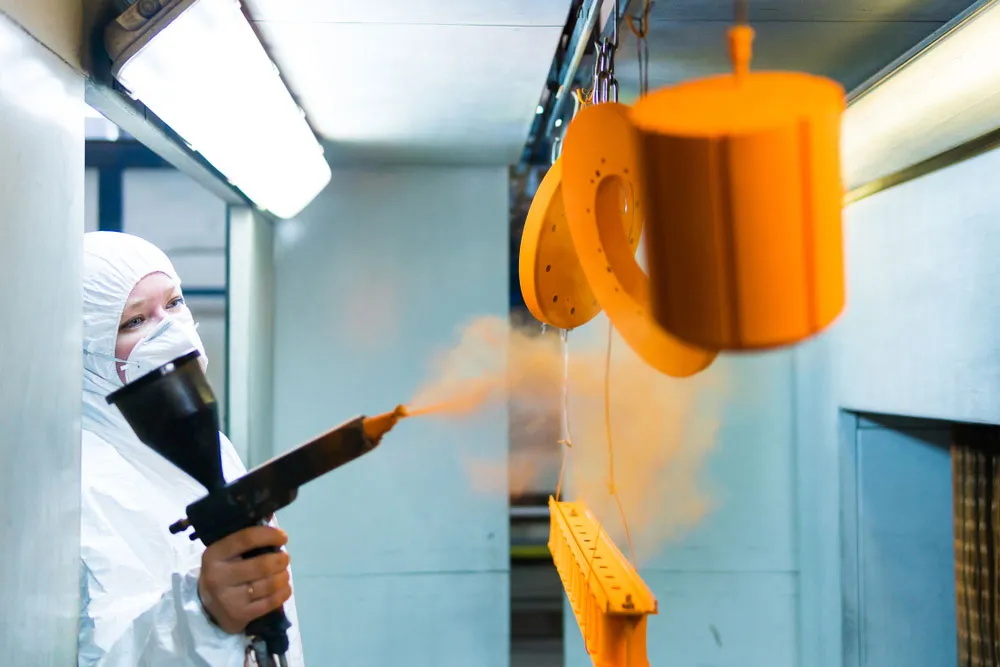
This article discusses five aspects of powder conservation, namely: film thickness control, one-time yield, profile powder loading rate, recycled powder management and hanging methods.
Preface
In short, electrostatic powder spraying uses a high-voltage generator to supply high voltage. The powder captures charges and becomes charged powder. Under the action of air flow and electric field, it flies to the pre-grounded profile, is adsorbed on the surface of the profile, and is baked and solidified in a curing oven to form a solid film layer. .
From the principle of electrostatic powder spraying, it is not difficult to see that the powder spraying process is first related to voltage, because voltage affects the strength of the electric field, thus affecting the powder loading rate;
It is related to the workpiece connecting the profile. The texture of the workpiece affects the conductive performance of the profile, thereby affecting the powder coating rate; it is also closely related to equipment, environment, etc.
Once we understand and control the powder spraying process to a certain extent, we will naturally focus on cost control, and the control of powder unit consumption is quite important.
Similarly, the amount of powder used is inseparable from several major factors that affect the powder spraying process. That is: voltage, workpiece, equipment, environment and method, etc.
These factors that affect powder unit consumption can be refined and classified into five categories: film thickness control, one-time yield, profile powder loading rate, recycled powder management and hanging methods.
1 Film thickness control
The most important way to save powder is film thickness control. The level of film thickness directly reflects the amount of powder consumed. If the film thickness is too low, it will cause flooding; if it is too high, it will cause orange peel on the surface.
If the film thickness control range is divided in detail, according to the powder characteristics, it can be distinguished from sand texture powder and light powder. Generally, the average particle size of new powder is 37μm~43μm. The particle size of sand texture powder is relatively large, and the powder coverage rate of the profile is High, so the upper limit of film thickness control can be lowered to save the amount of powder to the maximum extent;
The particle size of the glossy powder is small, and the coverage rate of the powder on the profile is low. You should try to spray it as thickly as possible to avoid flooding. Especially the white glossy powder has high transparency. If the film thickness is not enough, it will easily bloom and turn blue. Therefore, the glossy powder should be applied at the upper limit or Medium upper limit.
The ideal film thickness control range is a goal and an expectation. It is easy to say but difficult to do. To achieve this goal, workshop managers must focus on it.
At the same time, technical personnel must continue to supervise and monitor in real time, requiring front-line production employees to operate according to the process. Through the accumulation of experience in the powder spraying process of various types of powders and profiles, and continuous summarization, only in this way can the mature technology finally meet our expectations.
2 One-time yield
Production will inevitably produce defective products, and there will also be various problems, which will reduce our one-time finished product rate and require rework or even scrapping. In the end, repeating the machine or secondary production not only wastes powder, but also wastes time, manpower and material resources.
Especially the problem of batch size is a huge waste of powder and cost.
To ensure one-time yield, you must first ensure that the equipment is in good condition. Otherwise, various problems may occur.
For example, impurities in the surface treatment bath liquid will cause particles on the surface of the material, if the curing furnace is not cleaned cleanly, there will be furnace ash, and if the spray gun is not completely cleaned when changing colors, it will produce mottled colors, etc. Therefore, the equipment must be cleaned and maintained regularly to ensure that the equipment is in normal operation;
Then strictly control the product quality in each process, strengthen self-inspection, and ensure that no defective products are accepted or released;
Secondly, operations must be standardized, and all personnel must strictly abide by and improve the management system. Those who do not follow the process or operate in violation of regulations must be punished as a warning;
In addition, targeted measures should be taken for models with difficult births or models with frequent problems, and the process should be strictly controlled to avoid the recurrence of the same problem.
In short, great attention must be paid to all aspects of production, and no link can be ignored in order to effectively control the one-time yield.
3 Profile powder coating rate
The unit consumption of powder is directly related to the powder loading rate of the profile. Under the same time and powder flow rate, higher and lower powder loading rates directly affect the usage efficiency of the powder.
The powder loading rate of the profile is directly proportional to the voltage and current, and inversely proportional to the distance between the spray gun and the profile. Therefore, a certain voltage and current intensity must be ensured so that the charged powder can be well adsorbed on the surface of the profile.
The control of voltage and current should not be too high, otherwise it will cause electric shock marks on the surface, nor should it be too low, otherwise the powder charge will be smaller and the powder coating rate will be reduced.
For this reason, the powder should also have good electrical conductivity, so that under a certain voltage and current intensity, it can be ensured that the powder has enough electricity to be adsorbed on the surface of the profile.
When it comes to electrical conductivity, one thing that cannot be ignored is the cleaning of auxiliary equipment. Because we know that the principle of electrostatic spraying is simply that the pole needle at the head of the spray gun is used as the electrode, and the high voltage is supplied by the high voltage generator. When the powder is sprayed from the spray gun, it captures the charge and becomes a charged powder. The charged powder is adsorbed on the surface with the help of electrostatic field attraction. Profile surface.
Therefore, under the action of a certain electric field force, the conductive properties of hangers, hanging plates, and chains will directly affect the powder loading rate of charged powder. Therefore, these auxiliary equipment must be cleaned regularly and must not be covered with oil and powder dirt, otherwise it will affect the conductive performance of the profile and reduce the powder coating rate.
The distance between the spray gun and the profile must also be controlled. If the distance is too close, gun marks will be produced. If the distance is too far, the powder coating rate will be reduced. Adjust the optimal distance. Adjust the distance between the spray gun and the profile according to this optimal distance to ensure the profile. Under the premise of surface quality, the powder coating rate can be effectively improved.
4 Recycling powder management
Recycled powder is the powder that is not sprayed on the workpiece after the powder is sprayed once, and is recovered by special recycling equipment.
The main feature is that the content of coarse and fine powder is higher than that of normal powder, and the coarse powder has a large particle size, which may cause surface particles. The fine powder is easy to agglomerate and cause spitting, and the recycled powder has poor fluidity and poor powder loading, so it is generally not recommended. Spray directly.
However, the amount of recycled powder produced is huge. If it can be utilized, the powder savings will be very considerable.
Regarding how to use recycled powder correctly and rationally, the management of recycled powder is very important, and generally should include the following points:
(1) Generally, recycled powder cannot be sprayed directly and must be mixed with new powder. The mixing ratio must be determined according to the surface effect and quality requirements;
(2) The recycled powder should be used as early as possible. It is best to mix it with new powder while producing it. Generally, if the recycled powder is stored for more than three months, you should check whether the powder has agglomerated;
(3) For flat products, if the surface requirements are relatively high, an appropriate mesh screen should be used before use;
(4) For metal powder products, pay attention to the consistent proportion when adding recycled powder to avoid color difference;
(5) Among the mixed color powders, generally recycled powders contain more coarse powder components, so it is required to use a suitable sieve to screen them before use;
(6) When using a larger proportion of recycled powder, appropriate additives can be added to improve the fluidity and powder loading rate of the powder;
(7) Maximize the first powder application rate and reduce the generation of recycled powder, such as increasing the hanging density of workpieces, maintaining good grounding, adjusting the conditions and position of the spray gun, etc.
The above are just the basic principles in the management of recycled powder. The specific situation should be analyzed in detail. The use of recycled powder should not be vague or careless, because if you are not careful, it will cause batch defects, so that the recycled powder will not be effectively used. It also wastes new fans and wastes costs.
5 ways to hang materials
The amount of powder used and the quality of the surface effect are also closely related to the way of hanging materials. If the materials are not hung properly, powder will be wasted at best, and defective products will be produced in batches at worst. This is a huge waste of powder and cost.
The position for punching and hanging materials should be determined according to the model of the material and the decorative surface. Make sure that the decoration faces the spray gun. Materials with slots and corners should be slotted and cornered against the gun. First, the conditions for the corners of the slots to not be exposed must be considered. Control the film thickness for spraying.
If the material is not hung properly, causing the slot corners to be exposed, rework is required, and the powder sprayed on the front is wasted;
If the groove corner is facing the gun diagonally, the powder loading rate at the groove corner will be low, and more powder will need to be used to ensure that the bottom of the groove corner is not exposed. The film thickness on other surfaces will be very high, which also wastes powder.
Before producing each model, the density of the hanging material should also be carefully considered, because if the material is hung densely, it will increase the primary powder coating rate, but it may also make the side film thickness lower and cause panting;
On the contrary, if the density of the hanging material is too thin, it will reduce the primary powder coating rate, and may also cause the side film thickness to be too high, causing orange peel. Therefore, it is necessary to conduct detailed analysis of most common types of materials to select the best hanging material density and form a standard.
6 Summary
Lean production is the goal of each of our enterprises and also our responsibility, and cost control is quite important. For the powder spraying production workshop, powder saving is the core of cost control, and of course it is also the direction that we need to focus on and work hard on.