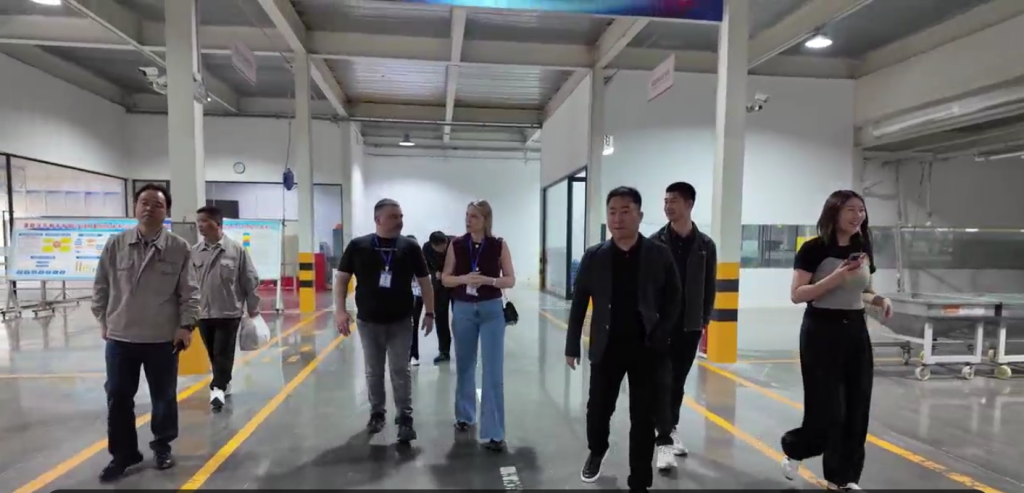
1.Visit Factory
Accompanied by the company's leadership team, the customer delegation visited the company's production workshop, R&D laboratory and quality inspection center, and observed the entire process of powder coatings from raw material screening, formula development to automated production and finished product testing.
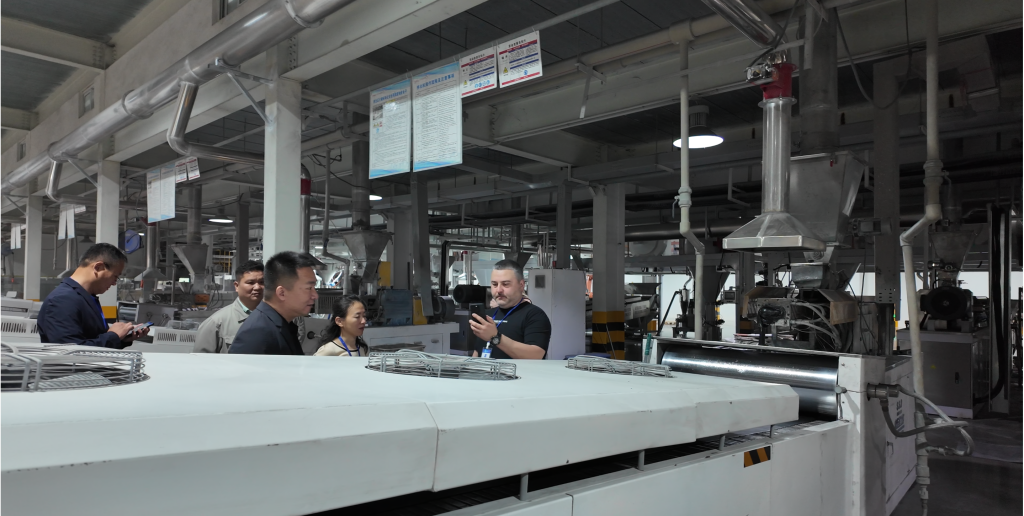
Production workshop: Visit the fully enclosed automated production line and learn about core processes such as electrostatic powder spraying and high-temperature curing. Customers highly recognize our company's large-scale production capabilities.
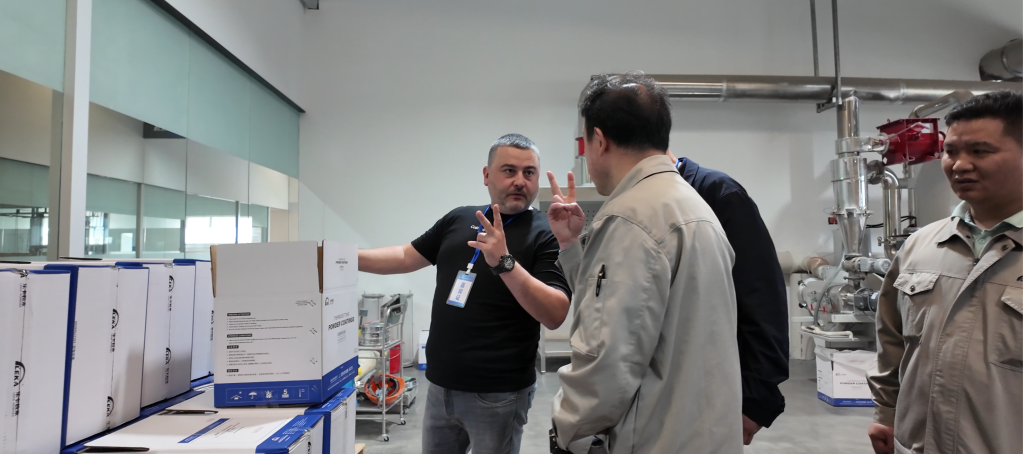
R&D Center: Focus on displaying environmentally friendly powder coatings, weather-resistant metal powder coatings and other technical achievements, highlighting the company's core competitiveness driven by innovation.
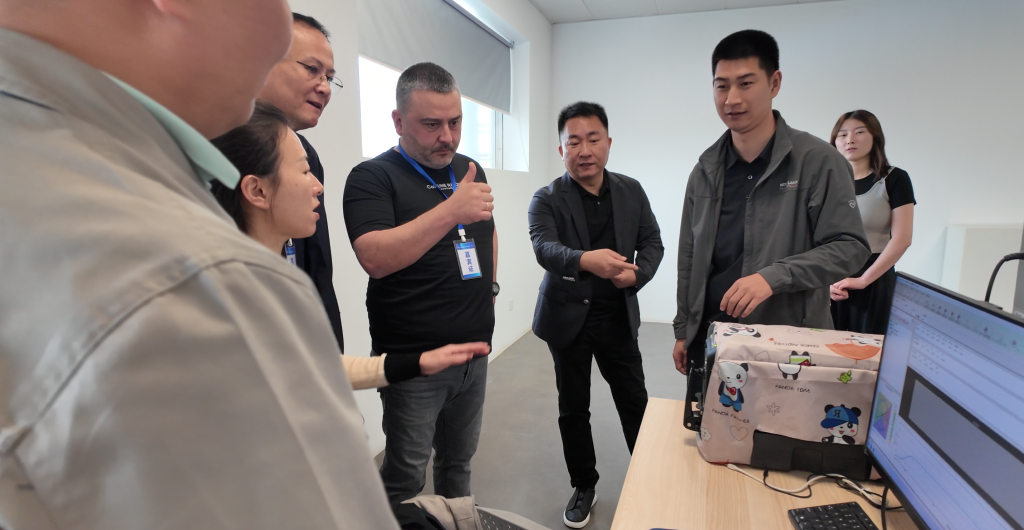
Quality Inspection Laboratory: Demonstrating the company's strict quality control system in line with international standards through demonstrations such as powder coating thickness test and weather resistance test.
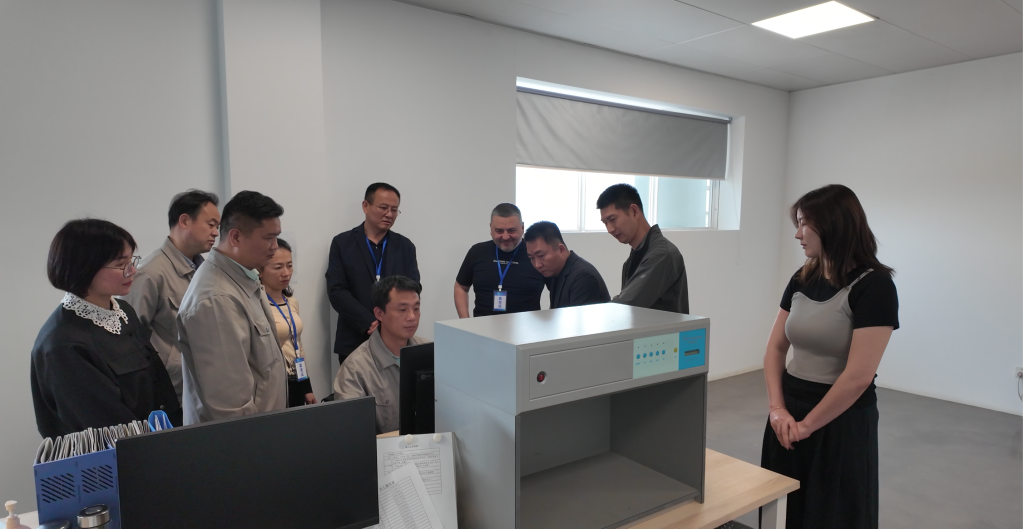
2. Discussion meeting
At the discussion meeting, the two sides had in-depth exchanges on the future all-round cooperation:
Customer representatives fully affirmed our company's "customer-centric" customized service model and appreciated value-added services such as after-sales guarantee.
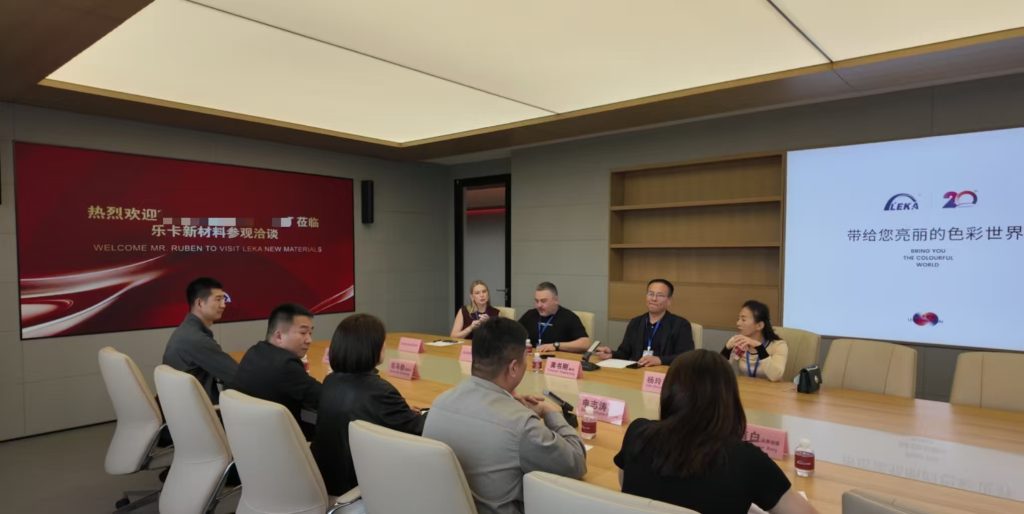
Every visit from a customer is a transmission of trust and a driving force for progress. Leka Powder has always embraced industry partners with an open attitude, and fulfilled its corporate mission of "bringing you a bright world of colors" with its technical strength and ingenuity!
